A great leap forward with DRAG technology
IMI Critical Engineering’s Chief Technology Officer, Mike Semens-Flanagan, reflects on the past, present and future of DRAGTM technologies.
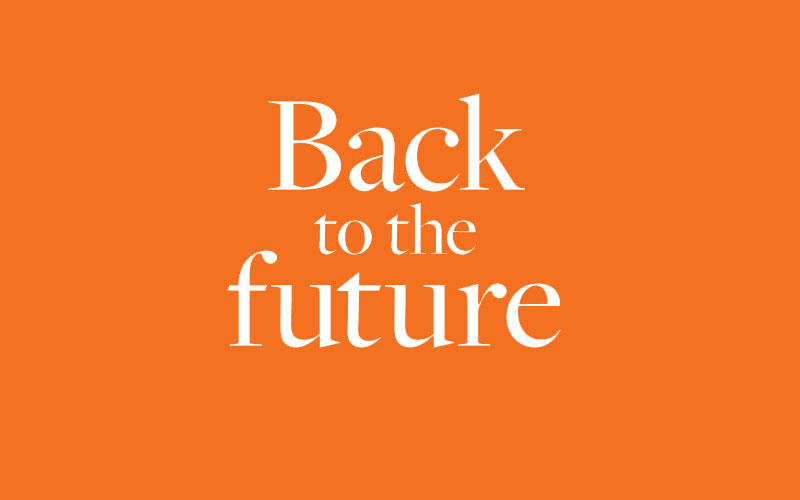
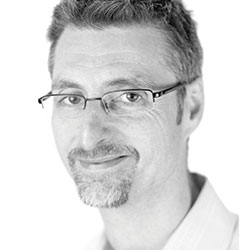
At that time, severe service valves were not that advanced – there was minimal flow control and corrosive fluids shortened the lifespan of equipment dramatically. The challenge was to control very high fluid velocities caused by pressure reduction – if pure oxygen fluid flow is not kept low, it will oxidise metal like an acetylene torch. DRAGTM technology was a truly innovative approach to managing destructive fluid flow velocities.
DRAGTM flow technology divides the flow of a fluid into many streams, creating multiple tortuous paths through which the fluid will pass. These create long laminar flow streams with high frictional drag forces, which cause the pressure drop. Mr Self went on to found the company that is now IMI CCI, designing, building and patenting the world’s first multistage control valve in 1967. Capable of handling high-pressure liquids and gases including, oil, steam, natural gas, petroleum products and chemicals, DRAGTM technology has revolutionised the valve industry, and the practices of end-users, designers, and manufacturers of flow control solutions.
Fast-forward to 2018, and DRAGTM technology is undergoing further innovation, thanks to the possibilities unleashed by the Industrial Internet of Things (IIoT) and the advent of additive manufacturing, aka 3D printing.
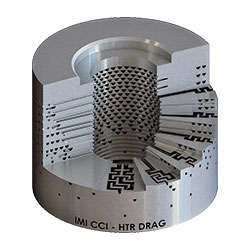
The IIoT is already opening up new possibilities. By building sensors into valves, we can collect real-time information on the performance of valves in critical applications and use the data to build predictive models for the future, potentially improving a valve’s safety, performance and efficiency. IMI Critical is already trialling ‘smart’ valves with customers, allowing monitoring of valve performance remotely. Within the next decade, ‘smart’ valves will become mainstream products.
Meanwhile, additive manufacturing opens up new ways to conceive of and design valves. While successful for smaller valves in low pressure applications, manufacturers are working hard on applying the technique to the much larger valves and more challenging materials used in high pressure critical applications. IMI Critical has already commissioned valves using components made by direct laser sintering, and there are exciting possibilities to make DRAGTM even better for our customers’ applications.
Fifty years after it was invented, DRAGTM technology still sets the standard today for fast and precise flow control. By harnessing the power of the IIoT and 3D printing, DRAGTM technology will set the standards for tomorrow too.
About
Part of IMI plc, IMI Critical Engineering is a world-leading provider of critical flow control solutions which enable vital energy and process industries to operate safely, cleanly, reliably and more efficiently. Employing around 4,000 talented people, the company operates a global service network with over 20 manufacturing facilities in 16 countries worldwide. It draws on extensive technical knowledge, engineering design capability and application experience to create custom-designed products offering unrivalled durability, safety and performance. www.imi-critical.com
Follow us
Advertise
Free e-Newsletter