What challenges are you overcoming with the current supply chain crunch?
The supply chain is currently experiencing a crunch, with shipping delays, price increases and logistics issues. What are EIC members doing to overcome these issues and thrive in an increasingly challenging operational environment? Energy Focus puts the big question to four members
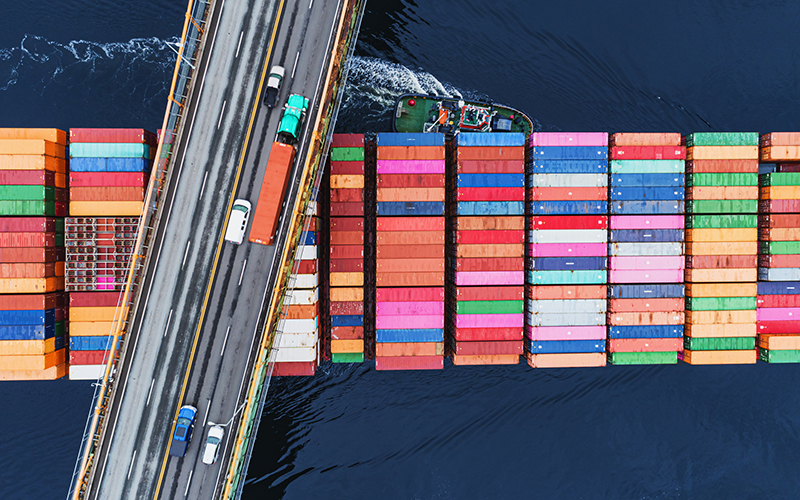
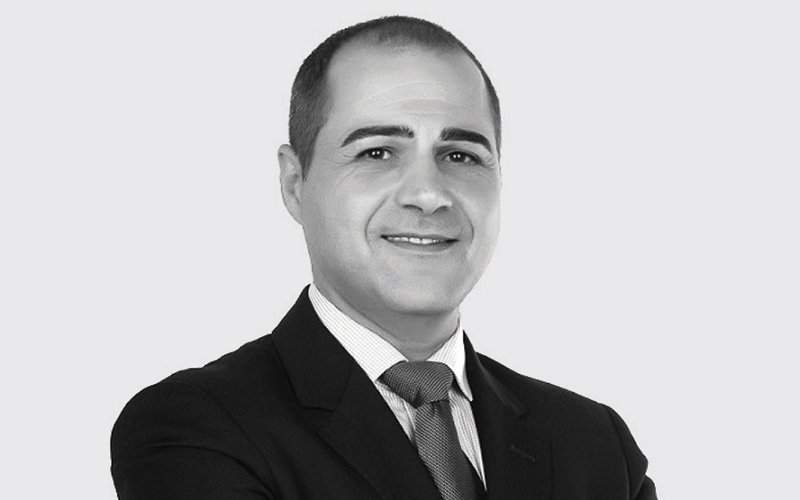
AAL Shipping is a global multipurpose shipping operator. Since COVID-19 emerged, stricter health and safety measures in ports and terminals and the rise in demand for basic goods and commodities have led to congestion issues and prolonged idle time.
Port terminals and cargo storage areas are full in many ports, causing delays to discharge and load operations and cargo readiness. This impacts our schedule, and congestion charges are being levied on shippers for access to some of the busiest ports. Our procurement of cargo lashing equipment and spare parts is being delayed and failing to meet delivery times while vessels are in port.
We constantly have to change the allocation of our vessels
We carry complex, multi-million-dollar heavy-lift project cargo, requiring specialist handling. Every cargo is different, as are stowage and engineering plans. It has proven difficult to schedule and execute vessel attendance of necessary shore personnel due to port restrictions and delays. This is increasing dependence on vessels’ masters, officers and crew, and remote communications systems. However, our services have operated uninterrupted during the pandemic and delivered a dependable solution for shippers and project owners.
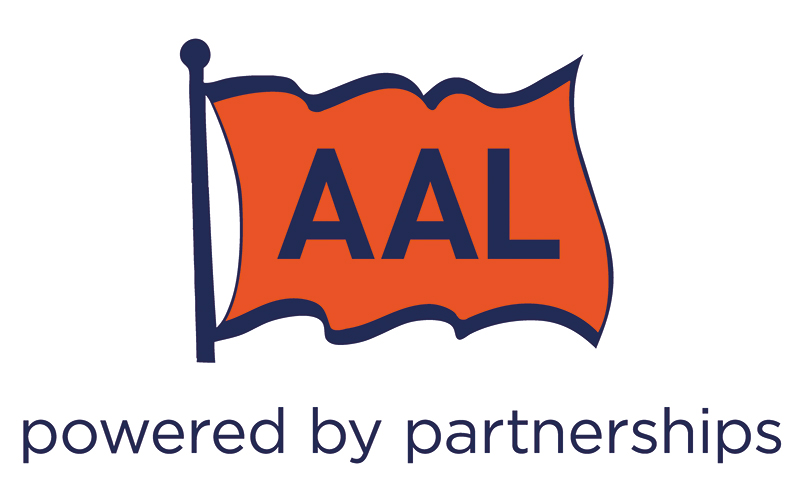
Planning future cargo employment for our fleet has been difficult. To optimise performance and deliver economies of scale, we constantly have to change the allocation of vessels and mitigate points of delay.
AAL Shipping is a project heavy-lift, breakbulk, steel, dry bulk and general cargo ocean transport operator. Since 1995, it has delivered solutions for industries such as energy, mining, construction and agriculture. AAL operates one of the sector’s largest heavy-lift fleets, serving scheduled monthly liner operations between Europe, Middle East, Asia and Oceania; regular trade lane services connecting the Americas and the rest of the world; and tailor-made tramp sailings globally.
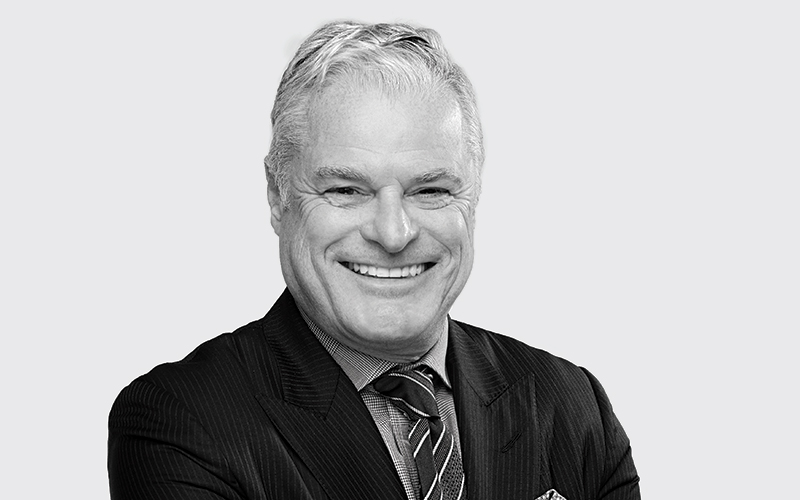
Focusing on project logistics within Africa and the Middle East, we have felt significant delays in several large size projects.The macro forces affecting the industry include reduced oil and gas production in Africa as investments in sustainable energy sources soar. The disruptive shocks from COVID-19 are also still being felt across the region, with Africa having been hit extremely hard – the impact has been vastly underestimated, with both cases and deaths in Africa significantly undercounted. There are also upcoming presidential elections in Angola, Kenya and Senegal – three countries supporting significant infrastructure projects.
We continue to look for ways to optimise efficiency in our processes
In addition to this, we are facing exceptionally high ocean freight rates caused by port congestions due to a lack of resources in some of the world’s largest ports, increased fuel prices, and shipping lines investing in more sustainable methods of transportation. And while costs are rising in the supply chain, clients and shippers want the cheapest price on paper – which is not necessarily the ultimate cheapest rate at the end of the day.
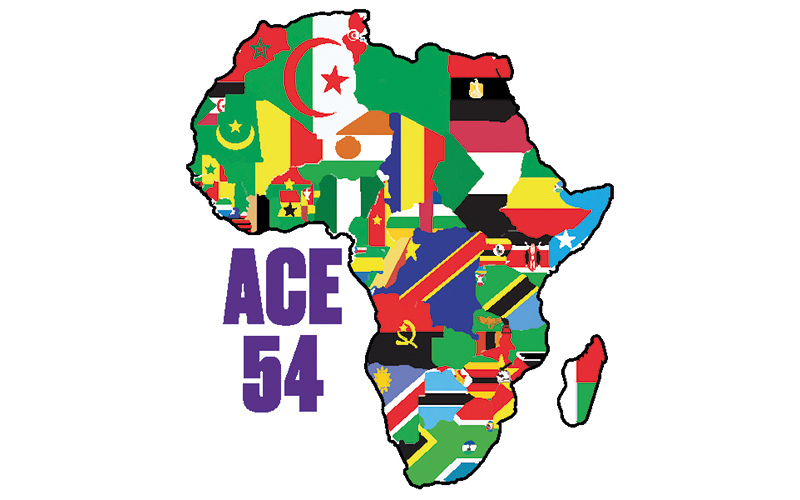
To mitigate against these challenges, we continue to look for ways to optimise efficiency in our processes and improve performance by being hands-on, so we can become the conduit for success for our global clients shipping to Africa and the Middle East.
ACE 54 offers shippers and consignees more options and a competitive edge in-country on the African continent. This concept provides technical information and best pricing for project destination services in the five African regions. The company has expertise in oil and gas (mid and downstream), renewables, mining, nuclear, hydro power, rail and infrastructure.
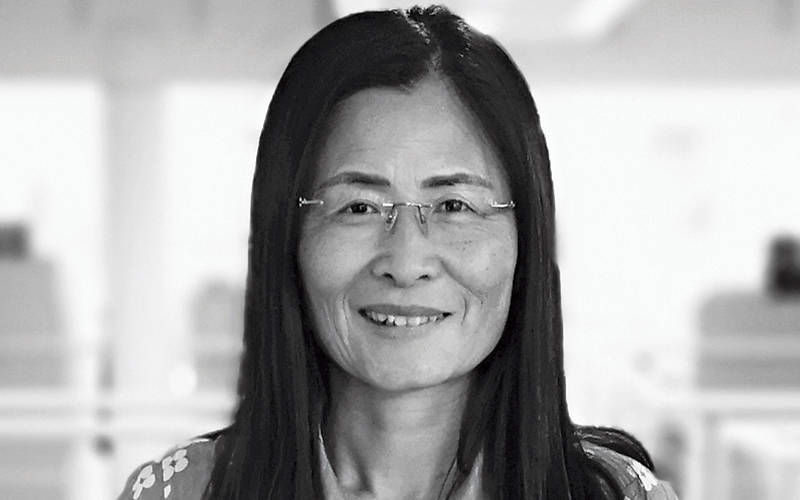
Despite the pandemic further compounding supply chain issues, Atmos International (Atmos) is fortunately a technology company, with services that can be delivered remotely. An area the supply chain crunch has impacted, however, is our leak and theft detection hardware.
For example, our non-intrusive instrumentation, such as Atmos Eclipse, is an important part of our customer’s leak and theft detection strategies, combining software and hardware to provide a complete solution.
Atmos’s R&D department has been constrained by parts shortages impacted by the pandemic and changes in customs regulations. Microchips, for example, are in high demand and manufactured in limited quantities. Ensuring we have sufficient stock before completing electronic designs, rather than buying for a ‘just-in-time’ manufacturing delivery, is one of the ways we overcome this.
R&D is flexible when it comes to changing difficult-to-source parts that are non-integral to meeting safety certifications. Good parts are also reused rather than being scrapped, not only to minimise wastage but also to put them back into circulation.
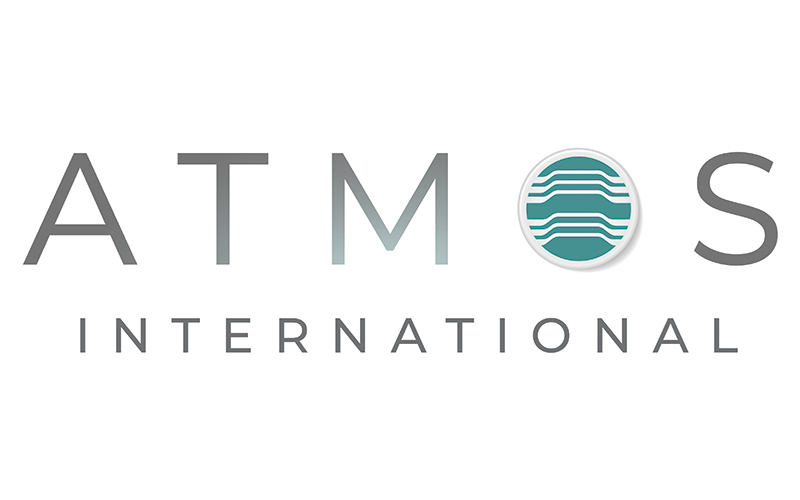
Overcoming these challenges meant we were able to deliver large-scale hardware projects at the height of the pandemic. For one customer, we delivered and installed over 50 Atmos Eclipse units across 38 sites.
Atmos International is passionate about technology, innovation and customers, aiming to deliver the the industry’s best pipeline leak detection, simulation solutions and customer service. More than 1,500 pipelines and 60 countries within the oil, gas, chemical, water, aviation and mining industries benefit from its technology.
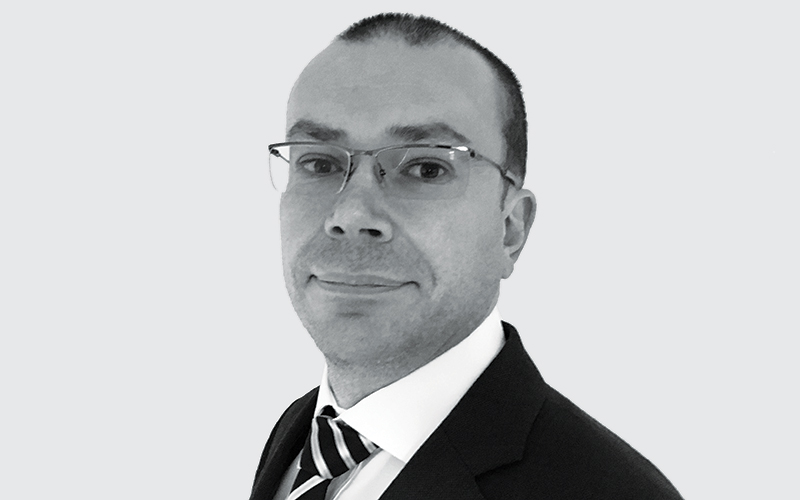
The challenges faced by supply chains are unprecedented and may represent a new normal. Brexit, COVID-19, protectionism, conflicts and extreme weather have contributed to a disrupted supply chain.
R&D is flexible when it comes to changing difficult-to-source parts We have developed strong internal networks to share intelligence and resources
Flexibility, adaptability, networks, collaboration and change-orientated individuals are key enablers for world-class organisations to thrive in today’s landscape. At Proserv, our supply chain can be global, regional and local. We therefore deploy appropriate strategies that support our operations, customers and stakeholders to deliver maximum value.
We have developed strong internal networks to share intelligence, resources and best practice, and through our Supply Chain Talent Development Programme we are providing Proserv’s future supply chain leaders with the necessary tools to succeed year on year.
Collaboration to address extended lead times through improved forecasting, the sharing of strategies and partnering are key to future growth. We recently signed a collabor

Proserv’s dynamic and committed supply chain team is front and centre in supporting our own energy transition. We have great confidence in our people and processes to maintain high levels of performance, no matter what challenges we face.
Proserv is a global controls technology leader, delivering solutions for infrastructure across the energy sector. Proserv’s mission is to harness its expertise and experience to innovate technologies that will improve the reliability, optimise the performance and extend the operational life of key assets. Proserv’s solutions encompass subsea and topside controls, holistic cable monitoring, SCADA systems, intervention workover control systems, sampling andmeasurement. Its technology strategy is focused on energy’s future and the company aims to reach net zero carbon by 2050 or earlier.
Image credit | iStock
Follow us
Advertise
Free e-Newsletter