UK technology helps buoy US offshore action
Paul Gallagher at SNC-Lavalin looks at how UK expertise is helping the US unlock its marginal fields.
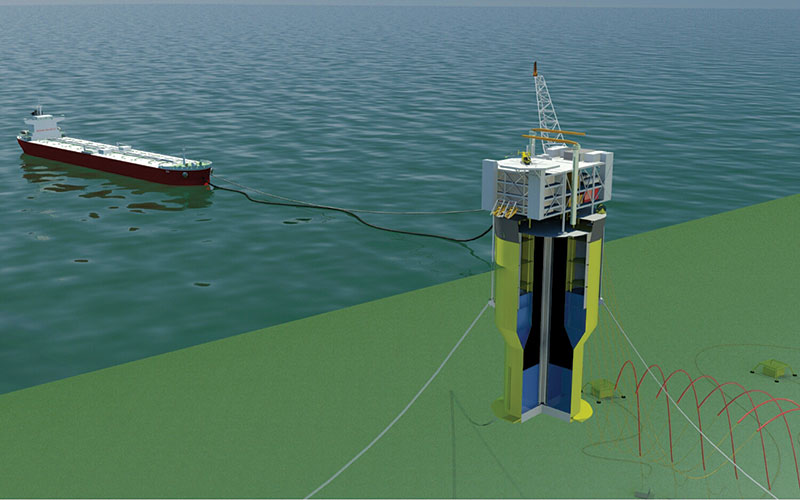
Pre-2014, the term ‘marginal field’ had become synonymous on the UK Continental Shelf (UKCS) with often low exploitable reserves (typically less than 25m barrels) and an estimated field life of 5–10 years. For such fields, investment in permanent facilities is not justified without taking risk on future tie-backs or potential hub developments.
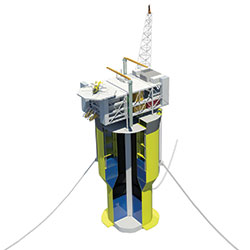
Driving North Sea innovation
Looking back to 2010–14, Atkins, a member of the SNC-Lavalin Group, worked for a number of clients for whom conventional production facilities were found to be uneconomic when applied to marginal fields.
With oil at US$65 per barrel, a common pre-2014 benchmark, marginal fields might only generate net present value of up to US$1.5bn, which put significant limitations on OPEX and CAPEX. Indeed, after exploration, drilling and well completion (D&C) costs were accounted for, CAPEX for the remaining production facilities might be squeezed to as little as US$300m if breakeven were to be achieved in three years. These constraints provided a drive for innovation in areas such as:
Increasing relevance of tie-back – to minimise both CAPEX and OPEX, tie-backs to a nearby host are often the first option for marginal fields if they can be negotiated.
Use of remotely operated normally unmanned facilities – this has continued to gain momentum since the oil price crash of 2014–15, but remains a subject for ongoing development.
Simplifying topsides process to reduce CAPEX – for example, with a single stage of separation combined with gas engines for power. Such simplifications, however, have implications for production efficiency and gas management.
Managing gas – for stranded fields, gas re-injection attracts additional CAPEX and OPEX, and gas-limited oil production can result in a significant fall in the net present value of the field reserves.
Shifting CAPEX to OPEX by use of leased facilities – reliance on leased floating production storage and offloading vessels (FPSOs) have grown significantly over the last decade, not least as it provides potential for risk sharing for smaller producers.
Novel floating production facilities – new concepts featuring elements of the above innovations within an inherently re-usable form, such as unmanned production buoys and compact FPSOs, both ship-shaped and more novel solutions (Figure 1), have all been developed.
Currently the ‘small pools’ (discoveries of less than 50m barrels of P50 reserves) identified by the UK Oil and Gas Authority, with a potential 2.4bn barrels of recoverable resources across the UKCS, are again driving similar calls for innovative solutions.
Transferable technology
For deepwater Gulf of Mexico (GoM) developments, exploration, and D&C costs are significantly higher than for the majority of the UKCS. With D&C costs ranging between US$100–200m per well, expectations on size of reserves and individual well productivity are of course greater. Nevertheless, economically marginal discoveries are just as likely as on the UKCS, as is the need for work to address technical and commercial challenges such as above if they are to be exploited.
Again, proximity to existing hubs and infrastructure can enable tie-back solutions, even if deepwater well completion and pipelay costs are high in comparison to tie-backs in the UKCS.
But where stand-alone facilities are required perhaps the most transferable technology is the wider adoption of re-usable floating production facilities to match short field lives, with similar types of risk sharing, lease-based, commercial models appropriate to the region.
The additional technical challenge, that of addressing hurricane events with smaller-scale facilities while maintaining low CAPEX in construction, can certainly be met given the experience of the industry and ingenuity of its offshore engineers.
But the key lessons that can be transferred are a mind-set that recognises the need to set a tough production facility CAPEX and five-year OPEX budget constraint in concept selection, along with the ability to manage the technical risks inherent in the innovations that make that possible.
By Paul Gallagher, Director for Field Development and Consulting in Engineering and Consulting, Oil and Gas, SNC-Lavalin
Follow us
Advertise
Free e-Newsletter