The rig of the future
Nicholas Newman drills down into next generation rigs
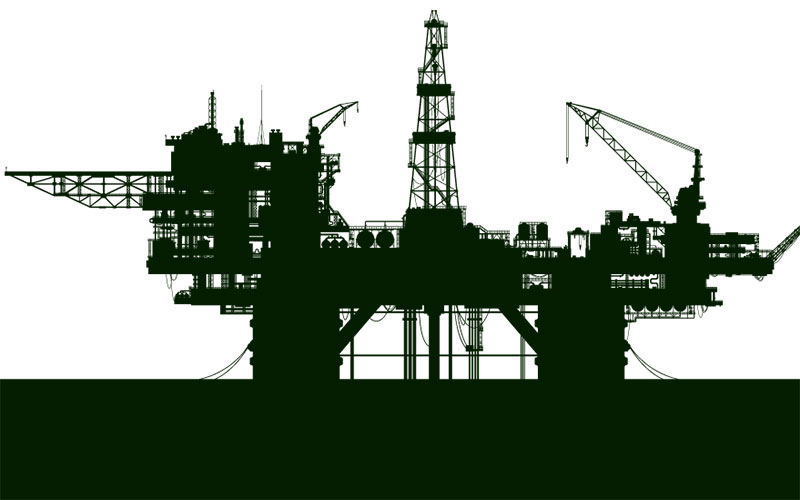
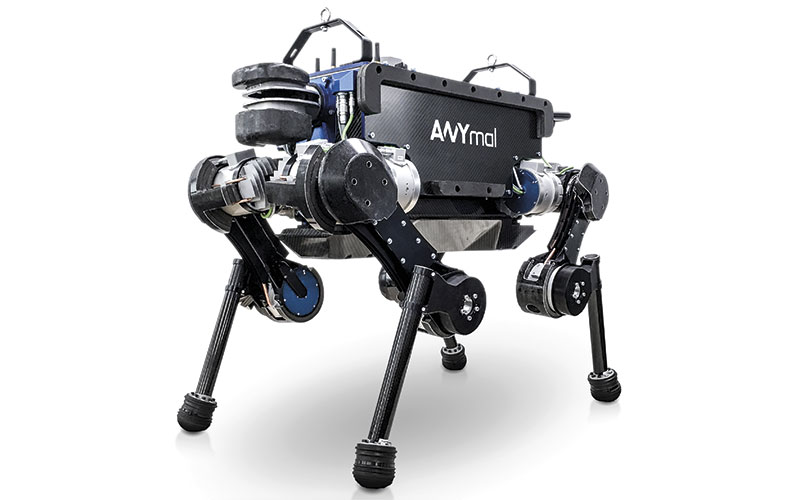
Traditionally, drilling into the earth’s surface is a very energy, labour and capital-intensive activity. However, this is beginning to change. Just as on land, on-site self-generation based on wind or solar to power rigs is beginning to take off. A typical North Sea or Gulf of Mexico rig currently operates with between 50 to 200 people according to the size of rig, but these numbers are set to fall with the application of artificial intelligence (AI) as rigs in deep waters become the preserve of AI-enabled robots controlled by humans in onshore control centres. Offshore rigs currently cost on average around US$650m, which is up to 20 times more than the average cost of land rigs – but the ‘industrialisation’ of rig design and production could bring down costs in coming years.
Smart drilling races ahead
The 2014 oil price collapse shocked the industry into retrenchment of capital expenditure, exploration and operating costs. On the positive side, however, the industry was forced into examining the new technologies coming on stream, including the Internet of Things, connected devices, cloud computing, standardisation and modularisation, 3D printing and now AI and automation.This has embedded further cost cuts and productivity increases as offshore exploration and production increases and orientates towards gas.
New rigs are increasingly being built with integrated sensor nets covering every aspect of the rig and the equipment used. Such sensors are designed to provide decision makers on the rig with better information to make operational decisions. For instance, sensors are being used in the drilling process to provide data on wellhead pressures, status of the drilling head and content of the oil and gas being extracted. In addition, we are seeing all aspects of the rig being monitored, including the location and health of the crew. This provides information for station keeping and even detecting structural concerns.
Robotic roustabouts
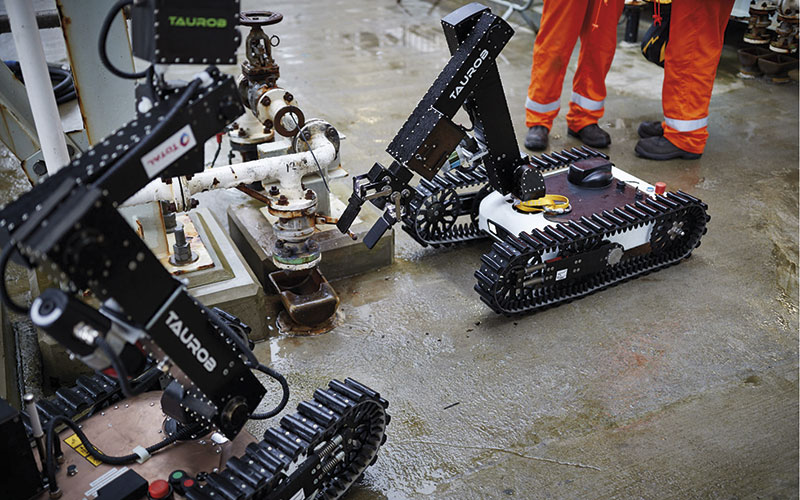
The vision of a rig operated entirely by autonomous robots is still in the realm of science fiction. Robots are still a rarity on offshore rigs and they are still controlled by people, often from remote locations. Ian Phillips, CEO, Oil and Gas Innovation Centre in Aberdeen, predicts that, ‘human assisted machines [robots] will be increasingly taking over many of the dangerous tasks’ on rigs. On the drill floor, for instance, automated drilling systems – also known as robotic roustabouts – are taking over many of the repetitive but hard labour tasks, such as applying the torque to pipe connections. Leading the field are companies like the US’s Nabors and Norway’s RDS. In the coming years, robots will be ubiquitous on rigs, able to work hand-in-hand with humans.
New technology maximises efficiency
Drilling is set to become more efficient. The combined application of cloud computing and big data analysis software is improving how drilling data is collected, monitored and analysed. Having accurate continuous measurement of mechanical, hydraulic and engineering drilling data is vital to balance fluid pressures, optimise the drilling process and maintain a safe operating environment. In fact, Colorado School of Mines suggests that by 2050, chemical industrial lasers could perhaps replace conventional drilling solutions. At present, though, major strides will have to be taken before the technology is commercially competitive with conventional drilling technology. Certainly, the use of lasers could improve extraction rates of fields that are currently less than 10%.
AI is put to the test
AI-enabled robots are currently being tested at Total’s Alwyn platform, located approximately 440km north-east of Aberdeen. These sophisticated robots are equipped with sensors that enable them to understand their environment, while algorithms allow them to plan, act and interact with humans and the environment. Other robots are carrying out visual inspections and detecting gas leaks as part of the US$47.5m Offshore Robotics for Certification of Assets (ORCA) programme, which is developing autonomous and semi-autonomous AI-enabled robots that are capable of inspecting, repairing, maintaining and certifying offshore-energy installations. This could become standard in the future.
However, the prospect of a fully automated offshore industry is a very big ask, given that AI is in its infancy. As Phillips cautions, ‘AI prior learning is a big challenge to teach machines, especially given the unpredictability of events’.
Designs on the future
As for the rigs themselves, it is increasingly likely the industry will make use of either floating or remotely operated automated subsea rigs fixed to the sea bottom. Total’s £3.5bn Laggan Tormore gas field off Shetland is credited with being the first example of a subsea-to-shore development. The field development is based on a combination of floating drill rigs to develop the wells and subsea automated rigs, which are supervised by a control centre on the isle of Shetland. Total’s pioneering effort is likely to be emulated by others developing deepwater fields.
Meanwhile, rig operators are looking at ways to reduce their greenhouse emissions. At present, most rigs depend on using on board gas-fuelled turbines to provide power. Two solutions to save space and cut emissions are being looked at by Equinor and other operators: the first is to directly link rigs to nearby floating wind farms, or directly by subsea cable to the mainland grid.
Changing role of the workforce
‘One thing is clear: there are likely to be fewer people working offshore,’ states Phillips – and the balance of the workforce is likely to shift from offshore towards onshore command and control centres. Technical advances will create the need for a new skill set of flexibility, creativity and problem-solving ability, and increase reliance on technology, software, and computer specialists.
Predictive maintenance and operations optimisation can help reduce:
- Material costs by 10%
- Finding and development costs by 5%
- Predictive analytics are expected
- to reduce downtime by 5%
Autonomous operations could help cut:
- Inspection and maintenance costs by 25%
- Drilling and completion costs (shelf and deepwater areas) by 20%
- Reduce downtime by 20%
Image credit | iStock
Follow us
Advertise
Free e-Newsletter