What does digital mean for the future of energy?
Digitalisation of the energy sector is gathering pace, improving asset performance and cutting running costs, writes Jeremy Bowden.
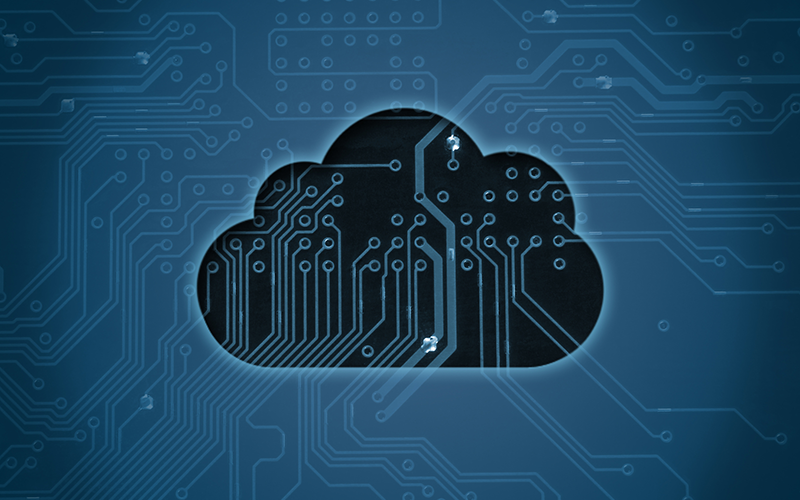
Both power generation and, especially, upstream oil and gas have been slow to appreciate the potential of digital technology. But now it is suddenly everywhere, and making a major impact. Digitalisation, and the subsequent analysis of data, is helping achieve sharp cost reductions through the optimisation of oil and gas production and field development, while it also enables predictive maintenance, which can result in zero downtime for energy installations – from offshore wind farms to gas pipelines.
Digitalisation involves the conversion of text, pictures or sound into a digital form that can be processed and analysed by a computer. Increased use of renewables, resiliency issues and sustainability concerns are just a few of the drivers behind the power sector’s digitalisation, which is progressing from the generating sets to the grid, and on into customers’ homes via smart meters. In the case of oil and gas, the weak oil price has forced the industry to critically evaluate spending, and digitalisation has proved itself to be an important factor in driving down costs in the North Sea and elsewhere.
Globally, annual offshore spending on digitalisation in the oil and gas sector is expected to reach US$17.8bn by 2022, and overall – including onshore and shale – the digital oilfield market could exceed US$30bn by 2020. But these spending figures are trivial compared to the potential upside. According to a recent report from the World Economic Forum, a full digital transformation in the oil and gas sector could eventually unlock about US$1.6tn of value globally – while Oxford Economics puts the added value at US$816bn or 0.8% of global GDP by 2025. Similarly, in another report last year, the World Economic Forum estimated that the power sector could capture US$1.3tn of value from digitalisation between 2016 and 2025.
Regarding oil and gas, the additional value comes from the optimisation of reservoir, well and facility development and performance, based on analysis of data from fully digitised systems. Further value is realised in both sectors by using virtual models generated from the data, which enables testing and assessing of the lowest cost performance and development options. Models can also be used to predict maintenance, cutting unplanned outages, while operational lessons learnt can easily be shared for mutual benefit.
Existing technologies to aid digitalisation | Emerging digitalisation technologies |
|
|
Source: Bloomberg New Energy Finance
Libraries and secure data
It’s not just your own data that is available in the new digital world. Much of the data that's not considered sensitive is accumulated by third parties and can be offered to the wider industry. ‘Cognitive learning can take in mistakes from all 450 platforms in the North Sea. We can all learn from each other and all the other rigs worldwide too. When something happens, all other installations learn from it instantly – in the same way that Google search learns every day from every search,’ said Gordon. ‘It’s now possible to turn data warehouses into libraries, which can be a relevant source for many people, helped by automated systems,’ he added.
Mr Namie said the flow of data needed to be handled carefully: ‘An oil company with rigs pulling in terabytes of data might not want to send it all back to the data centre – some needs to be kept local and processed at the edge. Some can be shared with other stakeholders or third parties. As data is moved around to get it to the right applications at the right time, there is also a necessity to enforce policies around data ownership, privacy and cyber security.’
North Sea retrofit
In the North Sea, digitalisation has contributed to recent sharp cost-cutting, and is making development of brownfield projects much easier, as options can easily be evaluated using accurate modelling.
‘Digitalisation of industrial processes have undoubtedly contributed to the 40% cost reductions in the North Sea since the oil price downturn,’ said Graeme Gordon, CEO of IFB and head of Scotland’s digital federation, ScotlandIS. However, with most of the assets already in place the job is not straightforward and involves a lot of retrofitting to unsuitable old equipment. ‘We are in a brownfield environment, so there are few fully fledged digital oil fields. An exception is Maersk’s Culzean platform, which is a relatively advanced digital platform that can collect and flow terabytes of data on and off the platform. By introducing core infrastructure upfront, as they have done, operating costs can be reduced by US$10m per year.’
Once the data is collected, it must be decided which bits are useful. Gordon said: ‘The average [North Sea] oil rig now produces about one terabyte of data a day. Around 90% of that is read-only, and is irrelevant so just passes through – it’s the 10% that is significant that you want. Then you turn that into intelligence using data analytics.’ He said the closest comparison to oil and gas was the space industry: ‘Space is most like oil and gas, as it’s very high risk when it goes wrong, plus long lead times, hostile environments – so everything needs to be checked in the background.’
For example, digitalisation can separately analyse production and choke points at hundreds of wells, accurately disaggregating production data so that conditions can be adjusted to optimise output at each well – increasing asset production efficiency in existing oilfields as a result. In a fully ‘connected enterprise’, assets can be monitored and optimised from anywhere in real time.
Phil Murray of Petrotechnics said collecting data from oil and gas installations was quite a messy and complicated process compared with, say, airline ticket booking, where all the parameters are clearly identifiable and laid out. Information on the flows and pressures of an oil field and wells, are far more complex and variable, making it trickier to systematically digitise. However, while each field is unique, common approaches can be adapted.
He said the biggest moves in digitalisation were not happening in the North Sea any more, but had moved downstream or overseas. ‘In the North Sea there is the drive and desire, but also a fear of being first, and disrupting production; there’s not much upside… Because it is a mature province, additional volumes are relatively small, there’s more complexity due to unsuitable older equipment – and more downside due to the added risk of disrupting production.’ As techniques are rolled out elsewhere – often by UK companies – case studies will become available, reducing risk and allowing North Sea operations to become ‘fast followers’, he added.
Nuclear digitalisation
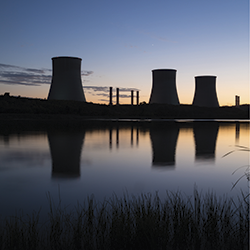
Digitalisation of a nuclear power plant involves installation of sensors, automation and analytics, enabling full lifecycle management. GE estimates its clients in the nuclear industry are now saving about US$2,000 per MWh in lower operation and maintenance costs because of digitalisation, helped by no unplanned downtime. In terms of the thermal performance of plants, GE is using big data analytics and closed-loop analytics.
‘In nuclear we’ve been focusing a lot on digital twins and how to get advantage from assets where there's criticality; how to keep those up and running, and how to get early warnings,’ said Sanjay Chopra, global leader, energy, at GE Digital. The earlier a warning is flagged up, the earlier you can start planning for the outage and ensure there is no unplanned downtime.
GE said it was looking at how to leverage data science and the cloud further to do ‘high-scale analytics’; creating interactive models to understand how generating sets are operating, and what can be done to optimise performance and minimise safety risks.
Creating value from data
The real test is how much useful information can be extracted from the data. Macario Namie, head of Internet of Things Strategy at Cisco, said, ‘The pace of change in the oil and gas sector has never been faster and to thrive, companies must become more efficient… And like most industries, the oil and gas sector is creating a huge amount of data. In order to derive value from all the connected things, this data must be extracted from its disparate sources and moved to applications that create business value.’
One way of creating value with the data is machine learning – a process in which software is used to search data, detect patterns and assess the likelihood of future failures. The software uses algorithms to monitor important equipment, and predict failures so preventive maintenance can be carried out. The data can also be used to create a virtual 'twin' that can be used to simulate different field development options, helping work out the cheapest and most effective course of action. For example, the degradation of wind turbine blades can be modelled using data from sensors that can pick up the slightest vibrations from a loose bearing or similar. You can then use the model to predict failure and intervene.
Mr Murray said harnessing the data to make better decisions was only possible when data was taken from different silos and converted into a ‘common currency’, from which tailored content could be supplied to different individuals based on their role. Effective use also requires a culture change throughout organisations, or a ‘human retrofit’ as Murray put it. This then allows operators to see where the risk is.
While cyber security concerns may be a rising consequence of the digital transition, utilising advanced analytics and simulation tools to optimise assets and operations has become an important factor in driving efficiency in today’s energy sector. Further digital oilfield advances, as well as an extension of digitalisation in areas like grid balancing and retail, are expected to keep the savings coming for some time to come.
Follow us
Advertise
Free e-Newsletter