Data: the new fuel for nuclear
The need for high quality data on a plant’s condition has never been more critical. Now is the time for nuclear to go digital, writes Will Newsom at Assystem
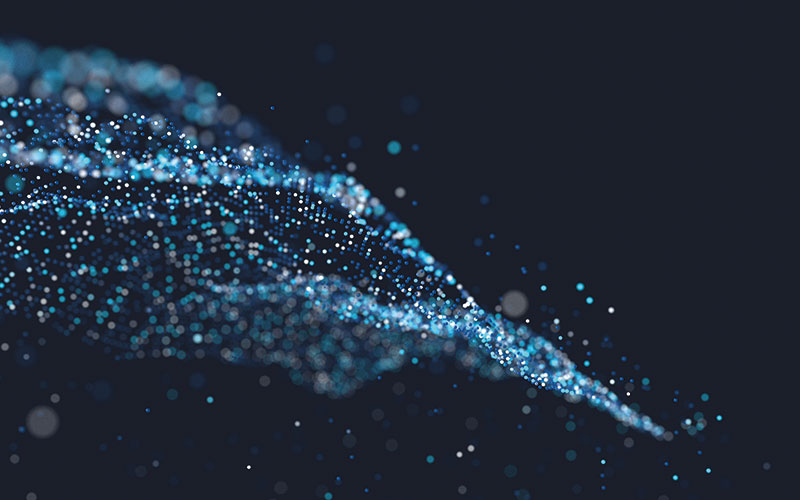
The need for plant upgrades, life extensions and decommissioning, together with Hinkley Point C heralding the start of a new era of nuclear power in the UK, present an industry ripe for realising value from Industry 4.0 technology. Connecting machines to physical systems to create intelligent networks, Industry 4.0 (the fourth industrial revolution) encompasses a range of sophisticated tools and data systems, including the Internet of Things, artificial intelligence and autonomous systems. One example of its effective use in the nuclear industry is how intelligent networks can predict failures and trigger maintenance events.
Machine vision
Machine vision is the process of providing automatic, image-based inspection and analysis for industrial processes. Machine vision technologies can provide a way to obtain automated, metric information from the world around us. For example, 3D cameras can be used to detect objects for autonomous robots to accurately grip and pick the object; or spectral imaging cameras can determine the chemical composition of items.
In the nuclear industry, machine vision can be used for remote inspections as part of periodic plant inspection or as part of a permanently installed condition monitoring system. The equipment is specifically designed to work in the harsh radiated environment.
Currently, most remote inspections are either subjective visual examinations undertaken by staff, or Non-Destructive Examinations (NDE). The visual inspections do not provide metric information. They are usually from low resolution cameras which provide poor quality images from which an assessor must determine if the item under test is suitable for continued operations or not. With NDE inspections, a highly trained operator must deploy equipment into a facility and usually must make physical contact with the item under test. This can be a difficult and time-consuming task. Machine vision can be a viable alternative to both methods as it can either be used in isolation or in conjunction with visual examination and NDE.
Safety and cost benefits
Through careful application, machine vision can provide many benefits to the nuclear industry. For example, instead of a visual examination, a laser line scan of structural steel can determine the size of surface-penetrating defects. This scan can be directly imported into a finite element analysis model where the effect of the defects can be analysed. Machine vision can also identify and classify defects in nuclear waste packages and determine the size of the package and the quantity of corrosion, as well as metrically quantify
the contaminants identified.
Ultimately, using machine vision, there is no longer a need to rely on subjective analysis or to contend with difficult equipment deployments. High quality metric data can be obtained on almost any remote plant item. This data can then be directly fed into a digital representation of the plant item where decisions can instantly be made on the effect of their condition. This allows us not only to speed up the inspection itself but also to speed up the post-processing and analysis of the inspection data. We are now able to obtain inspection data on items where this was once impossible.
The effect of using machine vision is that inspection times can be cut from days to minutes or weeks to hours, and it can identify areas of risk that are invisible to the human eye, enabling safer assessments of plant. It also reduces the amount of human contact required near the hazardous area, lowering the risks associated with maintenance in a radiated environment.
Making it happen
The more embedded machine vision and other Industry 4.0 technology become to the nuclear industry, the sooner we can realise the cost savings and safety benefits. Now is the time for the nuclear industry to seize the opportunity for innovation that is before us, innovating technology to suit our needs and creating our own digital revolution.
Picture Credit | iStock
Follow us
Advertise
Free e-Newsletter