New technology holds key to reaching carbon emissions targets
While carbon conversion technology is still in its infancy, Mark Stacey at Crown International spotlights one technology on the cusp of being commercialised
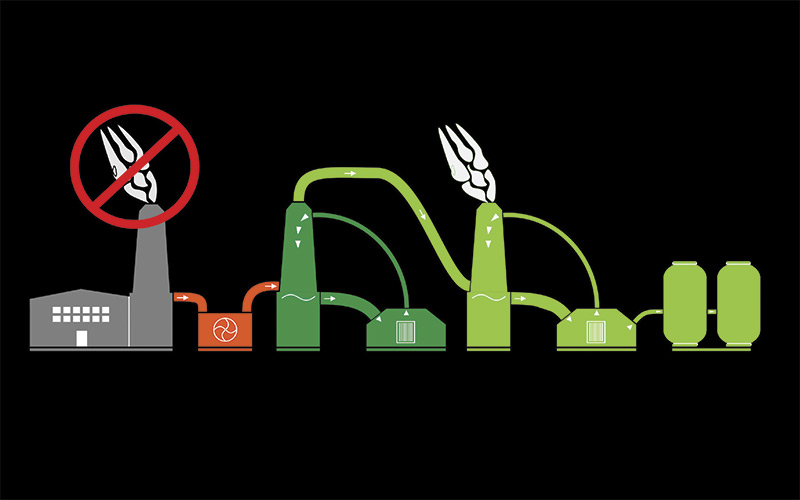
Crown International and Future Environmental Technologies Engineering have developed a ground-breaking carbon capture and exchange technology that uses flue gas CO2 as a feed stock for conversion into a range of valuable commodities, including formates and industrial alcohols.
Modular by design, the solution meets the Control of Major Accident Hazards Regulations Tier 1 requirements and can be installed and operational at a site within two years. Two initial trial projects (for the then-Department of Energy and Climate Change [DECC]) have captured 90% of CO2 (at 99% purity) and 85% of nitrous oxide (NOx) in flue gas emissions. Projections suggest the technology will deliver a return on investment within one year of operation, returning a total net present value cost per tonne of CO2 abated of just £47 (compared to £74 for monoethanolamine and £61 for advanced amines process).
So how does the process work?
The method utilises a two-stage carbon capture and conversion process (see Figure 1). In stage one, the flue gas is captured from the power plant’s flue stack at temperatures up to 270ºC. It is then cooled via a bespoke condensing economiser, which recovers heat and water and also acts as the input gas monitoring point. From there, the gas moves into a wash column, where a continually circulating metal-ion solution acts as the gas capture and carrying medium, removing and transforming any NOx and sulphur oxide present.
Once that process is complete, the conversion process gets underway. The remaining CO2 flows into a second-stage wash column where the gas is captured and separated. It then undergoes further processing via a patented methodology in which it is converted into high-grade hydrocarbon gas and/or by-products for on-site reuse or sale.
Opportunities exist to convert the output into harmless carbonates and bicarbonates for direct, safe deposit into the sea or into a diverse set of products, including formic acid, ethylene, methanol, syngas and, with additional feed materials, sulfuric acid. The remaining remediated cooled flue gas is then emitted from the wash column stack, which also acts as the output gas monitoring point. The process does not require elevated temperatures and pressures, nor does it produce any waste products that require disposal.
Commercial viability
The key to success of any carbon capture technology lies in making sure it is commercially attractive enough for energy companies to invest time and resources in adopting the solution. The DECC trial projects results suggest the benefits of this new technology warrants that investment.
Follow us
Advertise
Free e-Newsletter