Q&A: Floating wind comes of age
The UK is an attractive market for floating wind development. But for Roberts Proskovics, the engineer responsible for ORE Catapult’s floating wind project portfolio, a steady pipeline of projects and a supportive policy framework will be critical to catalyse growth and attract inward investment.
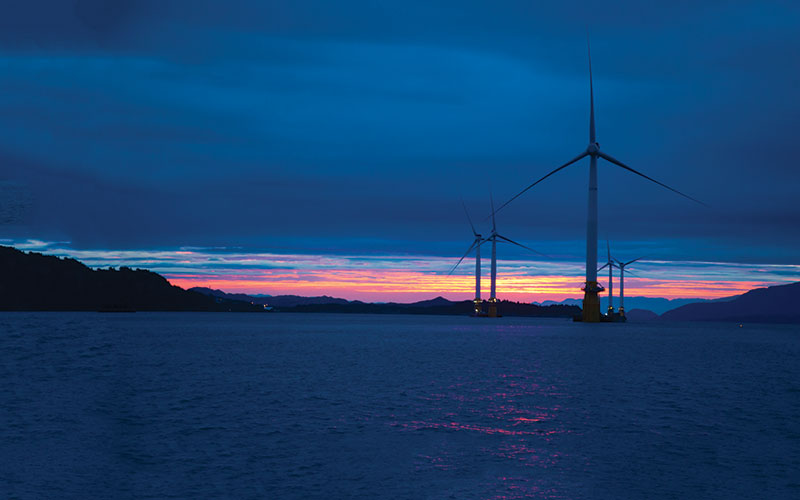
Q: The opening of Hywind Scotland was a real milestone for the floating offshore wind sector. What is now needed from government to help overcome commercial barriers and to support the next phase of floating wind?
A: The Hywind Scotland project benefited from the support mechanisms put in place by the government to help accelerate development of new innovative renewable energy technologies. The current support mechanism is due to run out this year and, currently, there is no new mechanism in place to build on the progress made to date. This means that, under current arrangements, future floating wind projects will have to compete for Contracts for Difference against other more developed technologies such as bottom-fixed offshore wind.
The key requirement for the sector in the UK is a route to market and commitment to a steady pipeline of projects, recognising that, at this stage of development, costs for floating wind are high relative to more mature renewables. This should be supplemented with policy measures which support the development of the UK supply chain in order to ensure the UK can reap the economic benefits as well as clean energy from deploying floating wind. It is also critical that sites suitable for floating wind are included in the next round of offshore wind development zones.
Q: There is an opportunity to make the UK the centre for this emerging technology. What is required from the industry to make this happen?
A: The UK already has strong oil and gas, and bottom-fixed offshore wind supply chains. Floating wind could tap into these, as there are many commonalities between these industries. However, there are components, processes and requirements that are unique to floating wind. Some can be tackled through targeted research and innovation, while others will require direct investment in the facilities to make these fit for floating wind (e.g. upgrading port infrastructure). There are also opportunities for collaboration between different segments of the supply chain to create more optimised, holistic solutions (e.g. anchors, moorings and substructures).
For the supply chain to invest in its facilities and in research and development, there needs to be a steady pipeline of projects. Currently, this does not exist, but a sector deal that includes floating wind would show industry commitment, which could be matched by government.
Q: To build a global industry the LCOE for floating offshore wind must be brought down. How can critical parts of the supply chain cut costs?
A: We have seen some good cost reduction in floating wind already (Statoil claims a 70% reduction in the capital expenditure per megawatt for the Hywind Scotland project compared with the original prototype); however, further reduction is required. We believe that the reduction will mainly come through scale (larger wind turbines, as substructures scale very positively; and fixed costs being split across a larger number of units – e.g. offshore and onshore substation, cables to shore, vessel costs, onshore facilities, fixed operations and maintenance costs and development), and maturity and innovation (further design optimisation, serial manufacturing, reduced installation times, mass market).
Q: What lessons can be learnt from other energy sectors to help the industry drive innovation and deliver a capable, competitive, and innovative local supply chain?
A: Bottom-fixed offshore wind, but more so oil and gas, has been very good in coming together to solve common challenges. The CRINE initiative of the early 1990s demonstrated how competing oil and gas companies could collaborate effectively to achieve critical cost reductions through adopting new approaches and culture. Floating wind is well placed to take advantage from the already developed industries for onshore and bottom-fixed offshore wind, and oil and gas by reusing already developed components and processes, and not repeating mistakes made in other industries.
Q: France and Japan are two lucrative markets for the expansion of floating offshore wind energy. How can UK suppliers leverage their expertise to become competitive in these emerging markets and indeed the global marketplace?
A: The starting point will be developing a domestic market where UK companies can grow and showcase their expertise. Investment and R&D should be focused on areas well suited to exports. This includes: high-value, easily transportable components such as electrical connectors; engineering and design expertise; remote monitoring and inspection equipment and techniques; and (eventually) artificial intelligence solutions. As well as leveraging their expertise, it may be necessary to partner with companies established in these markets and form trade links with the help of government bodies such as the Department for International Trade.
The UK is well known around the world for its ability to innovate and for the quality of its products. However, this often comes at higher cost compared to some other countries, and so a focus on cost reduction will also be critical.
Q: What technological innovations and developments do you expect to see in five years’ time?
A: With more floating offshore wind turbines being installed globally, the technology will be further proven, but more importantly commercially de-risked. The four pilot-arrays and the launch of a commercial tender in France will help to achieve this. Use of floating wind for directly powering marginal oil and gas fields, as investigated in the Wind Power Water Injection (WIN–WIN) project could also be proven. Additionally, we should see large 10MW+ wind turbines being rolled out; floating wind substructures being further optimised; new designs of holistic anchor-mooring-platform solutions developed; development of dynamic cables and wet-mate connectors with high power rating; and remote inspection.
Follow us
Advertise
Free e-Newsletter